Published by FLOW Mountain Bike 15 August 2016
In the coming weeks we're going to be handing out a spanking to a set of brand spanking new wheels from Wheelworks. This custom wheel-builder from Wellington, NZ is the only mob we've heard of offering a lifetime warranty on their builds, so they've clearly got confidence in their workmanship.
We got Wheelworks founder Tristan Thomas on the line to answer a few questions about why all wheels are not created equal, and to dispel a few myths around the oft-called ‘dark art’ of wheel building.
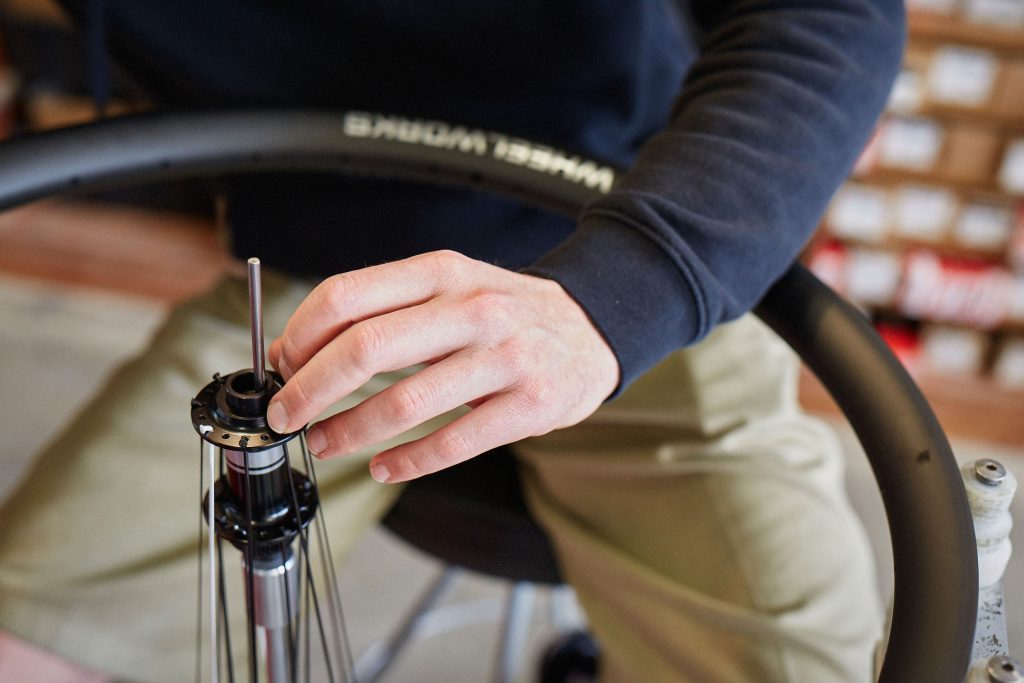
How every good wheel build begins.
We’re going to be testing the Flite Wide Carbon wheels, which boast a 34mm internal width. From our perspective, we feel that rim width can really transform a bike in so many positive ways. Given the performance benefits, why do you think it took so long for wide rims to come about?
We’ve been building and riding wide rims for about 5 years now and it’s great to see them become popular and mainstream. From our point of view there aren’t many downsides to rims with an internal width of 30 to 40mm, and as you know there are a whole lot of positives.
I think the delay with seeing these rim widths becoming adopted by the industry is that after the move from 26” to 29” and then 27.5” that most companies felt they’d already overloaded their customers and their supply chain with wheel changes and that the move to wide rim wasn’t a priority for them.
I don’t think we’ll see much change in rim widths over the next few years. I think that rims will go as wide as 40mm for 2.8-ish tyres but for everything from XC oriented 2.2” to enduro oriented 2.5” will use rims in the 30-40mm range. We’ve been running everthing from 33mm cyclocross tyres on 30mm rims and there really is zero downside to wider rims.
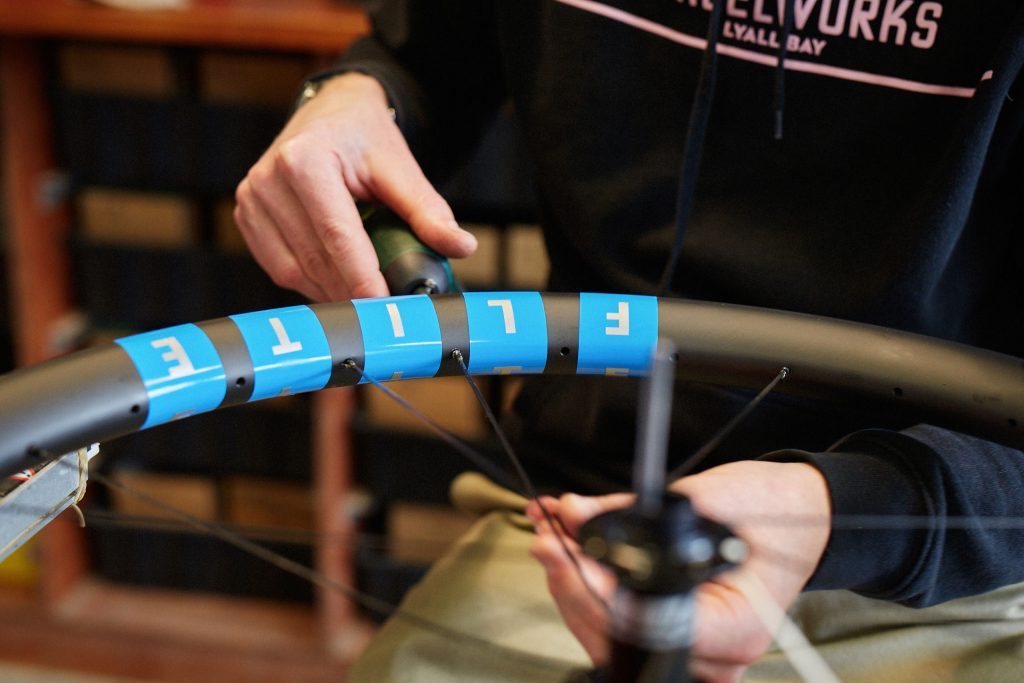
Just like with alloy rims, there’s a huge range of quality in carbon rims too.
Our test wheels are carbon. What are the most common misunderstandings, myths or mis-truths about carbon rims?
My big frustration is that all carbon rims, whether they’re good or bad, get lumped into this same category of “carbon rims” and talked about like they’re the same and this isn’t fair or accurate. There are plenty of good quality aluminium rims which are much better in every measurable way than a cheap carbon rim.
Modern, high-quality, carbon rims like our Flites are the lightest, stiffest, and most durable rims available. The only downside is that they’re more expensive than aluminium.
You also offer an alloy Flite wheel set. Can you have an alloy-rimmed wheel that’s as strong as a carbon-rimmed wheel? Are there any inherent limitations or advantages to an alloy rim?
Alloy wheels are far from dead and there is heaps of product development still going into them. Modern wide alloy rims are a big improvement on the narrow, flexy things of yesteryear. In general an alloy wheelset will be heavier and less stiff, but will be cheaper. Alloy rims tend to dent when they’re whacked…this can be a good thing and is why you see EWS racers using alloy, whereas good carbon will take a pretty serious beating with no damage at all but whack them hard enough and they will crack. In general alloy rims should be treated as a consumable item for an aggressive rider…they’ll dent and eventually have a hard time holding an airtight tubeless bead. Good carbon rims don’t suffer from these dents and will outlast alloy.
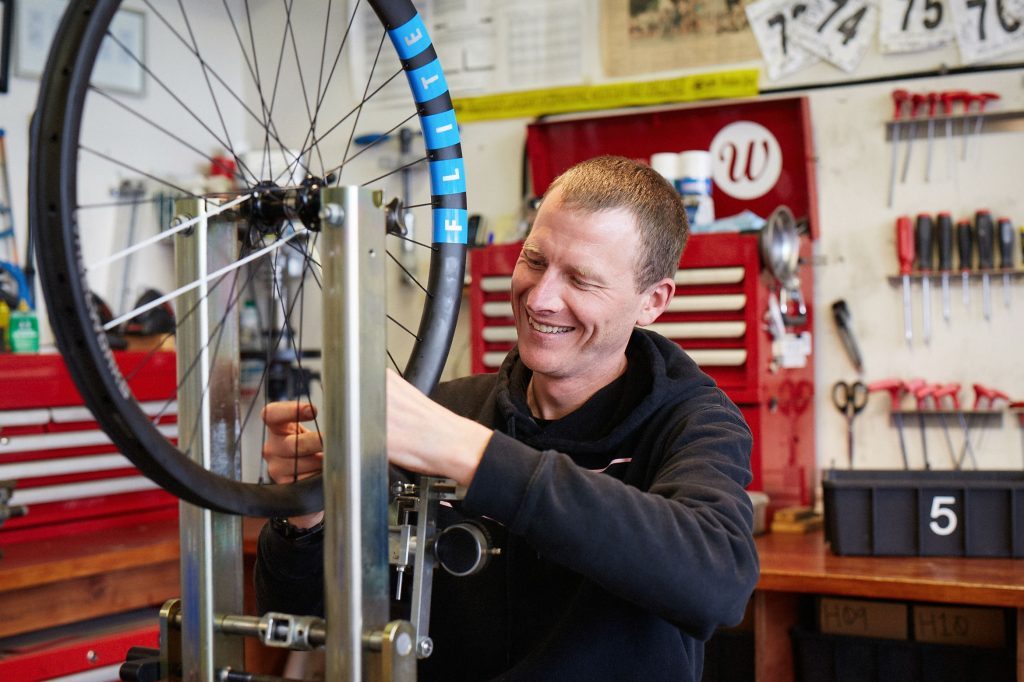
Strength, stiffness and durability are all very different attributes, even though they often get lumped together.
Where does a wheel actually derive its strength from? How much is a product of the rim versus the build quality etc?
Stiffness, strength, durability are three terms which get used and I think it’s worth clearing these up as they’re very different but often get confused.
Lateral stiffness is how much the wheels flex when loaded sideways during cornering, landing crooked (come on, admit it!) knocking off rocks or riding off-camber roots. A stiffer wheel provides a more direct, confidence-inspiring ride. A wheel which isn’t stiff enough is vague or mushy to ride. Once a wheel has ‘enough’ stiffness the rider won’t notice twice as much stiffness. I think of it like having a waterproof roof on your house: if it’s not waterproof enough then it will drip in the rain but once waterproofed it doesn’t matter if you double or quadruple that waterproofness as you’re still going to remain dry. How much lateral stiffness is ‘enough’ depends on the ride weight and style, and on their bike. Also worth noting is that a super stiff wheel won’t be noticed when clamped into a super-flexy fork with a flexy stem and flexy handlebar.
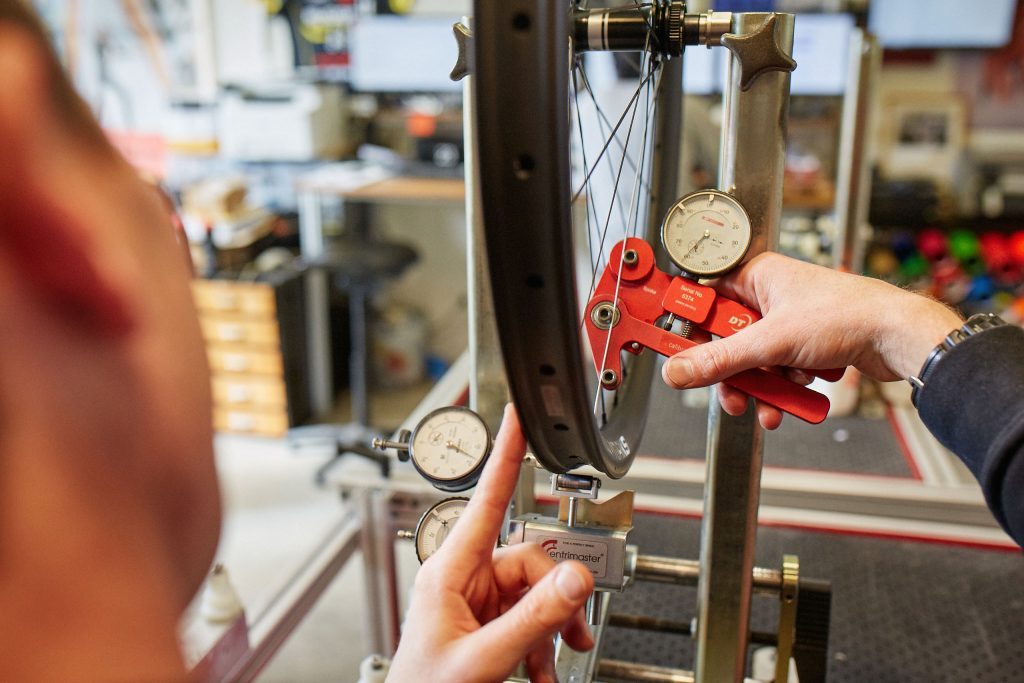
Higher spoke tensions don’t necessarily equate to a stiffer wheel, despite popular myth to the contrary.
Vertical stiffness is another myth. Wheels don’t flex vertically in any amount which could be significant. Your tyres have around 60mm of vertical flex so adding, say, 1mm of rim flex just won’t do anything.
Strength is how a wheel will respond to one, single, hard impact: A cased jump, a hard strike onto a root, etc. Strength mainly comes from the rim’s design and a good, strong rim poorly laced to a cheap hub will still be strong.
Durability is how well a wheel responds to prolonged riding and continued impacts. A wheel’s durability is much harder to measure and building durable wheels is not easy. This is where some of the ‘black art’ of wheelbuilding comes in and although no single silver-bullet will give you excellent wheel durability – there are plenty of small steps, custom tools, and minor tweaks that can be done during the wheelbuild process to increase durability. We’ve been doing this for over 10 years and wheel durability is a huge area of focus for me and the reason we’re able to offer lifetime guarantees on wheels.
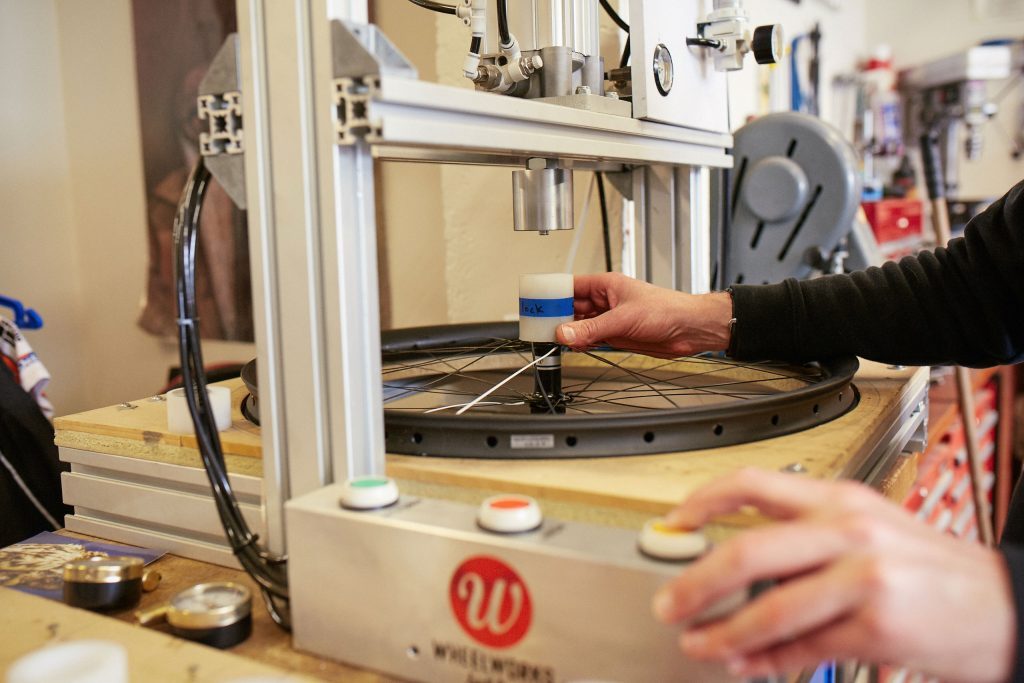
‘Grimlock’ is Wheelworks’ custom press that subjects wheels to forces far beyond what a rider is capable of.
We notice you offer a lifetime broken spoke warranty. How can you do this?
Because we’ve figured out how to ensure they don’t break! As part of every wheelbuild we measure the rim and hub and calculate the spoke length. We then cut spokes to the exact right length, down to 0.1mm accuracy, specific to that wheel to ensure we’ve got full thread engagement in the nipple. If the spokes are too short they’ll break the nipple, if they’re too long they’ll break at the first thread. When they’re the perfect length and combined with our other steps, we can guarantee they’ll never break.
There are two types of warranty: one where the manufacturer expects the product to fail and be replaced, and one where the manufacturer puts steps in place to nearly eliminate possibility of failure. We offer the second type of warranty and I’m extremely proud of the durability of our wheels.
You’ve mentioned to your ‘grimlock’ machine, which pre-stresses the wheel. Can you explain how it works and the importance of this process?
If you’ve ever ridden a brand-new bike you’ve likely heard a popping sound coming from the spokes as they settle in, unwind themselves, bend themselves slightly, and loosen off. With some hand-built wheels you’ll hear that they need to go back to the builder after they’ve ‘settled in’ to be re-tensioned and re-trued.
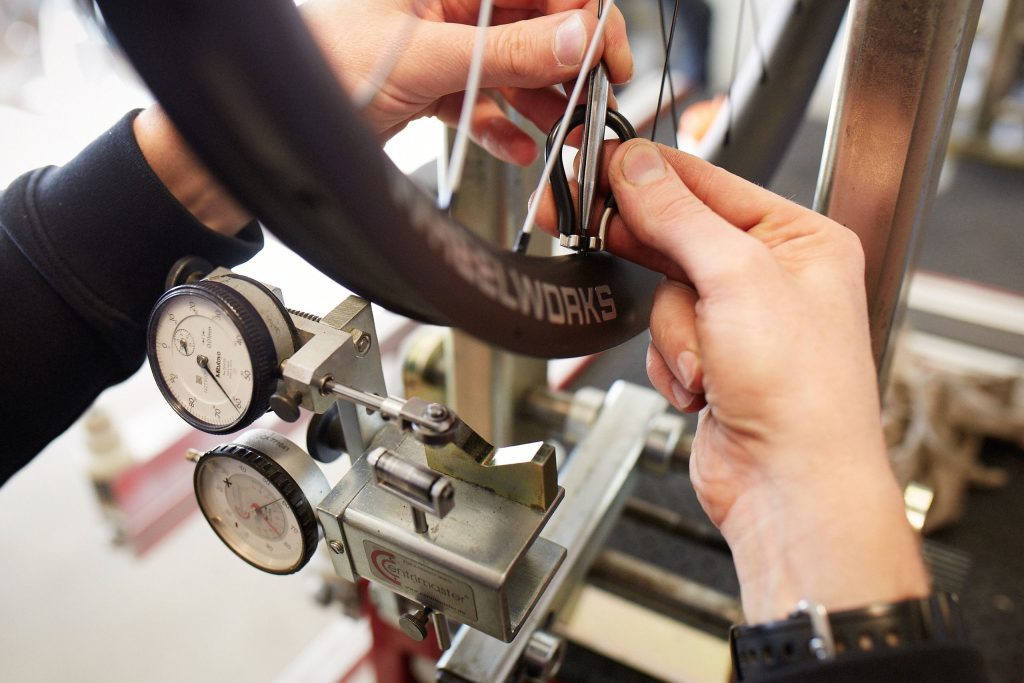
After Grimlock, the wheels go back into the truing stand.
Grimlock allows us to apply a vicious amount of force into the wheel in a really controlled way, and basically over-load the wheel well beyond what will happen when you ride it. The first time a wheel goes into Grimlock it loses about half its spoke tension so we need to re-tension and re-true the wheel. We alternate this process of re-tension and re-truing, and putting the wheel through Grimlock until the wheel comes out of Grimlock as true as when it went in. At that point the wheel has been stressed well beyond what a rider can do and we’ve got full faith that barring a huge crash the wheel will never go out of true.
Do spoking patterns really have an impact in the world of mountain biking? How do you lace mountain bike wheels and why?
There are a few little things that lacing patterns impact but nothing too significant. We lace most carbon rims with a 2-cross pattern which reduces the angle that the spoke enters the rim and helps with rim durability a little. We lace the rear wheels so that the ‘pulling’ spokes bring the crossing in towards the centerline under power to give a bit more derailleur clearance, but with modern 142 and 148mm dropouts being so stiff and modern 40-plus tooth cassettes this doesn’t have a significant effect for most people.

What is the next frontier for wheel development?
The area between Plus and non-Plus is pretty blurred at the moment and you’ll see that continue, but the industry will settle on 30-40mm rims for non-Plus bikes, 40-50mm for Plus sizes and those horrible 23mm rims will be a relic of the past like V-brakes.
Carbon rims will continue to drop in price and will be spec’d on lower-priced bikes but the high-end stuff will remain at a similar price.
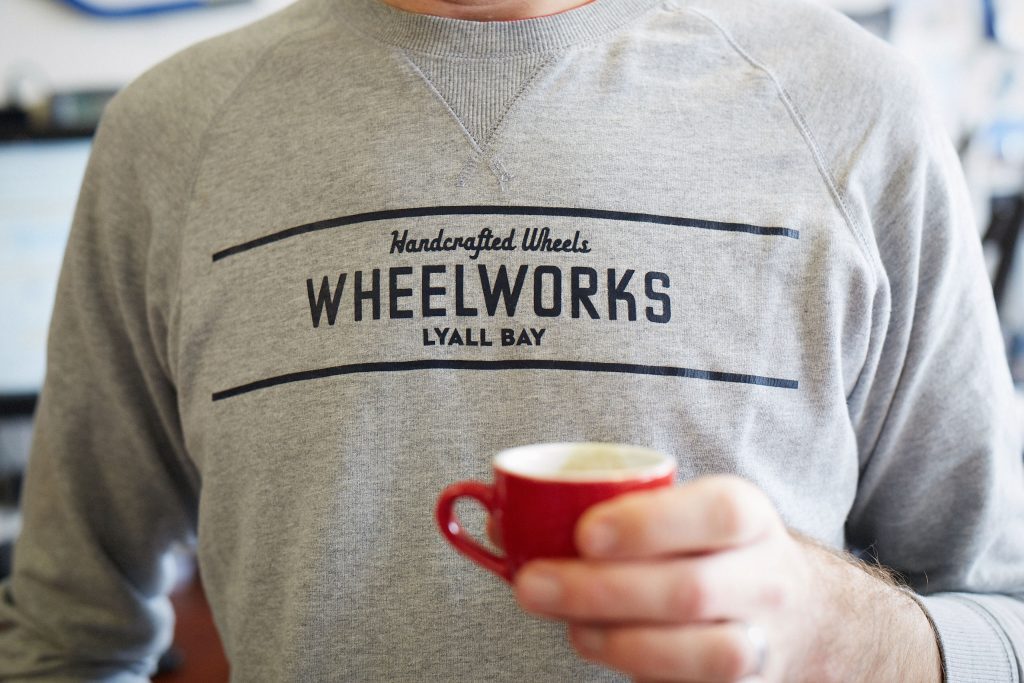
Short black? How did you know?
If you look at the holistic development of the bike I think that wheels are in front of the curve. I think we’re unlikely to see really significant changes to wheels in the next few years but there will be lots of development in tyres to make the most of wider rims.
Bikes which can accept both super-wide 27.5” tyres and 29” tyres will be increasingly common. What we’re seeing riders owning this type of bike can drastically change how the bike rides by carefully selecting two wheel and tyre combinations so they no longer have a need for an XC bike and a Trail bike and just swap wheels instead.
At the moment we’ve got a mess of axle ‘standards’ which are confusing for riders and make life harder for everyone in the industry from frame companies to dealers so we’ll see the industry settle on a single standard which works.
Thanks for taking the time to chat, Tristan! We’re looking forward to putting your wheels to work!
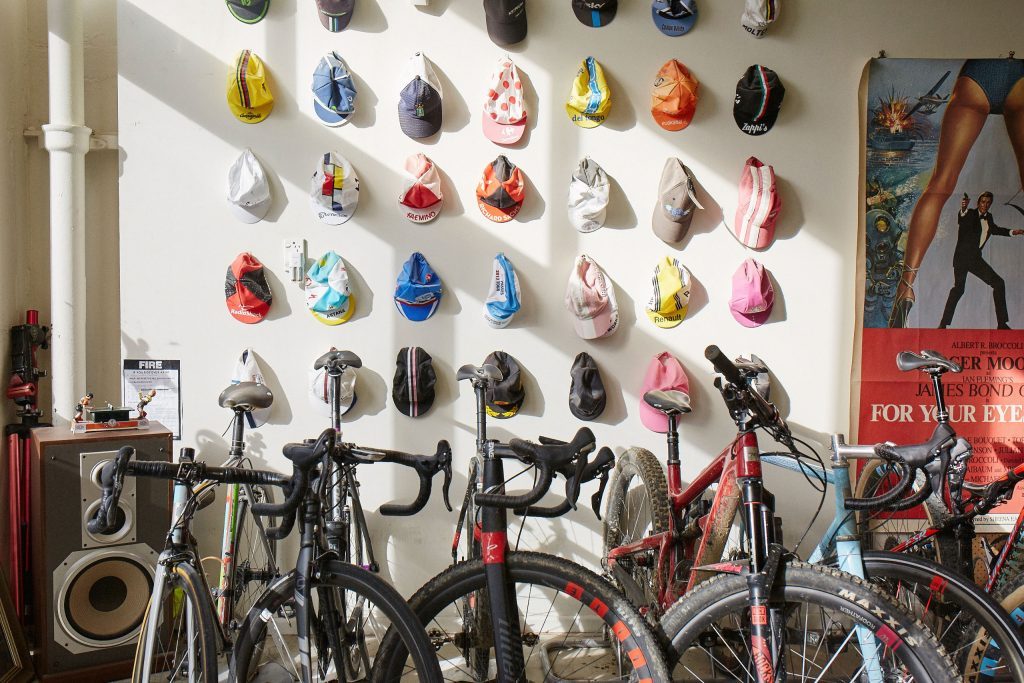