What makes us unique
Wheels built by Wheelworks are high performance, custom built wheels, for life.
Every step in the process, from the component selection and wheel design/solution, to the build and customisation, through to support and maintenance, has to work together to meet each customer's needs.

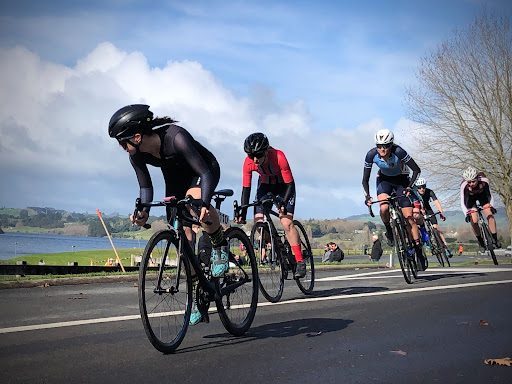
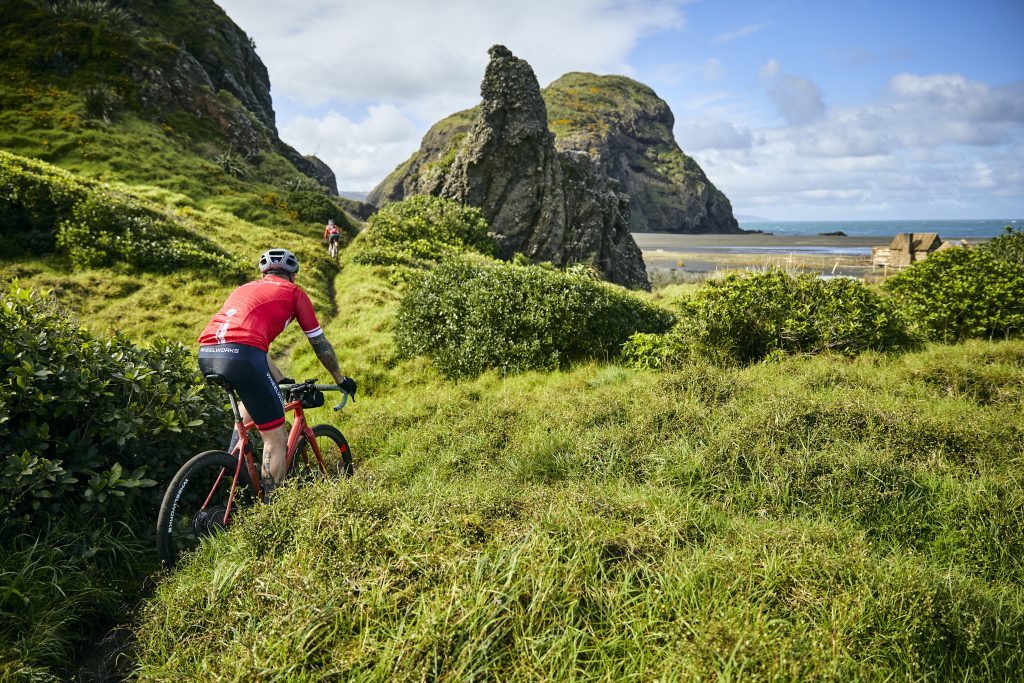
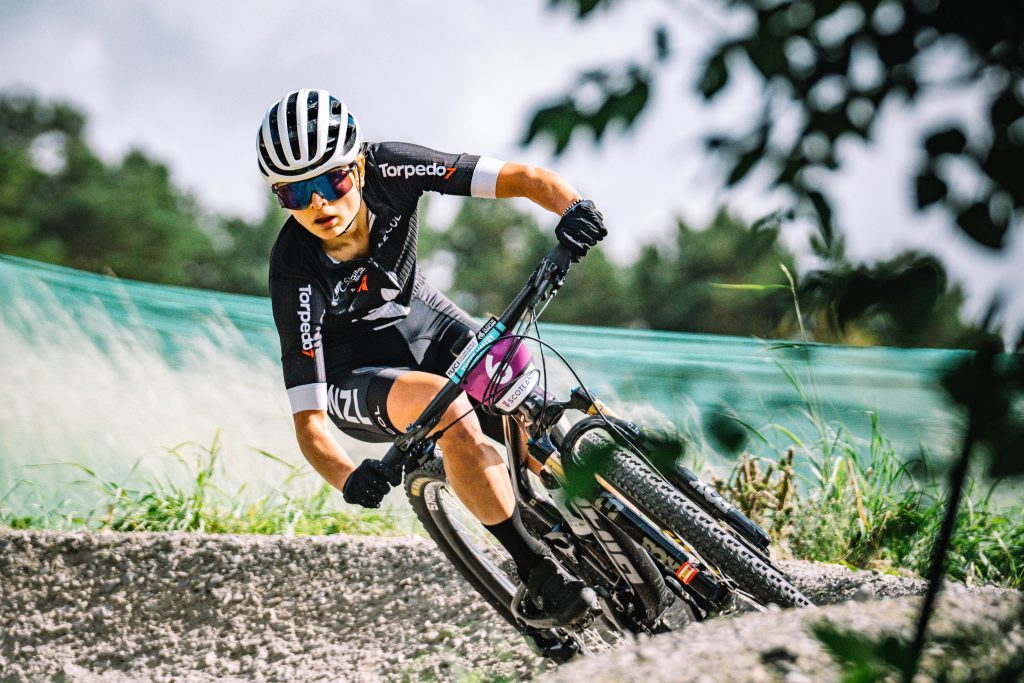
Personalised for you
Exceptional individualised service
Custom wheels start with thoughtful consideration of your needs and what's fit for your purpose. Built just for you, no other wheels will be as finely tuned as the ones we make you. It's about having a conversation and we've had thousands.
Each component is selected for the intended use, taking into account not just the individual components but also the way they interact. We also consider the long term use of the wheel and how it might need to adapt over time. We draw on our experience of building or servicing most of the wheel component brands in the market.
After recovering from a recent injury I finally got a ride in on the new Enduro carbon wheels. They feel great! My bike is more precise and playful, so epic! Thanks again super stoked!- Tom, Feb 2023
Just a quick note to say how much I LOVE my wheelset you built up for me a year ago. am enjoying my bike more and more and just wanted to congratulate you on an amazing product. You were right, when you told my husband “your wife will love the wheels”. I am thrilled with how the bike performs now and can’t wait for my next biking day.- Uschi, Jan 2023
Unique wheel number
Each wheel we build is engraved with a unique number and we keep detailed records dating back to the very first wheel we built in 2006 tracking details like spoke length, pre-stress procedure, and even what type of grease was used between the spoke and nipple.
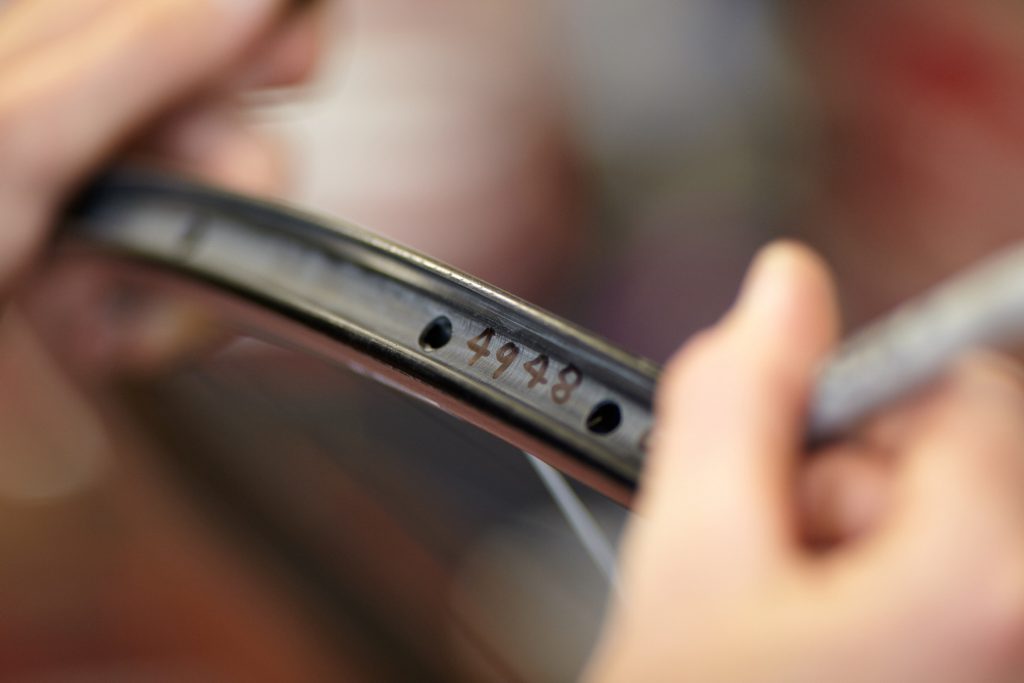
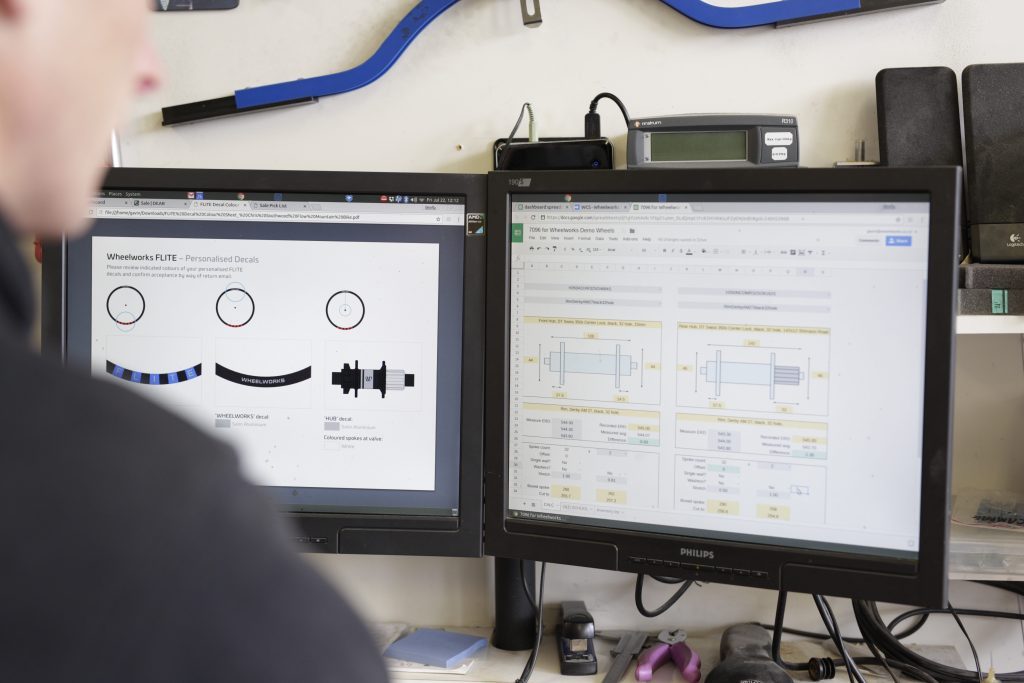
Add personal touches
Personalising your wheels might mean matching your bike, or intentionally not. Over the years we've matched wheels to corporate branding, beloved tractors, children's favourite colours - every kind of inspiration!
With options across rim decals, hub decals, coloured hubs, spoke colours and feature spokes at the valve, there's lots of ways to make your wheels unique.
Berd spokes can be dyed once built in almost any colour, pattern or design imaginable.
A peek behind the curtain
To share what we do and how we do it, we can send you photo updates of your wheels being built. How cool is that? You can choose either real-time photo updates or a post-build report - either way you’ll get an insight into why our meticulous wheel building process translates into amazing wheels with a lifetime guarantee.
You’ll be kept in the loop with how your decals are made, be able to see your wheels being laced and follow as the wheels are trued to one-tenth of a millimeter (that’s about the width of a human hair, by the way). These photo updates are an option for every wheelset we build - it’s our way of letting you peek behind the curtain and see the skill, effort, and tricks that go into every wheelset we build.
Cheers for the updates, I can see why your wheels are the best, so much attention to detail!
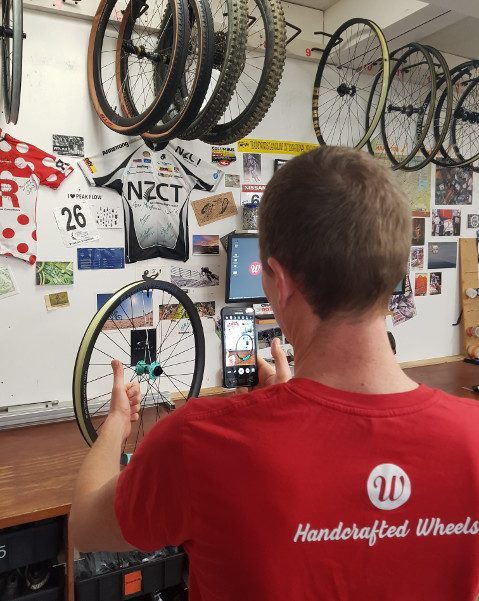
Innovative wheel building technology
Unlike the traditional bikeshop who occasionally builds wheels, we are solely focused on building excellent wheels and delivering world-class service. Our wheel-building process has been honed over many thousands of custom wheels.
We’ve studied the minutia of each and every step in the process to minimise error and inconsistency and maximise wheelset performance and durability. Our processes are so specialised that we’ve had to develop the tooling, machinery and software to build and maintain the quality of each and every wheelset.
If you're not measuring, you're guessing
We incorporated Islandix's excellent digital visualization tools into our process. Islandix lets us quantify exactly how true our wheels are, and helps us get them true with fewer spoke nipple adjustments meaning less in-built stress in the wheel.
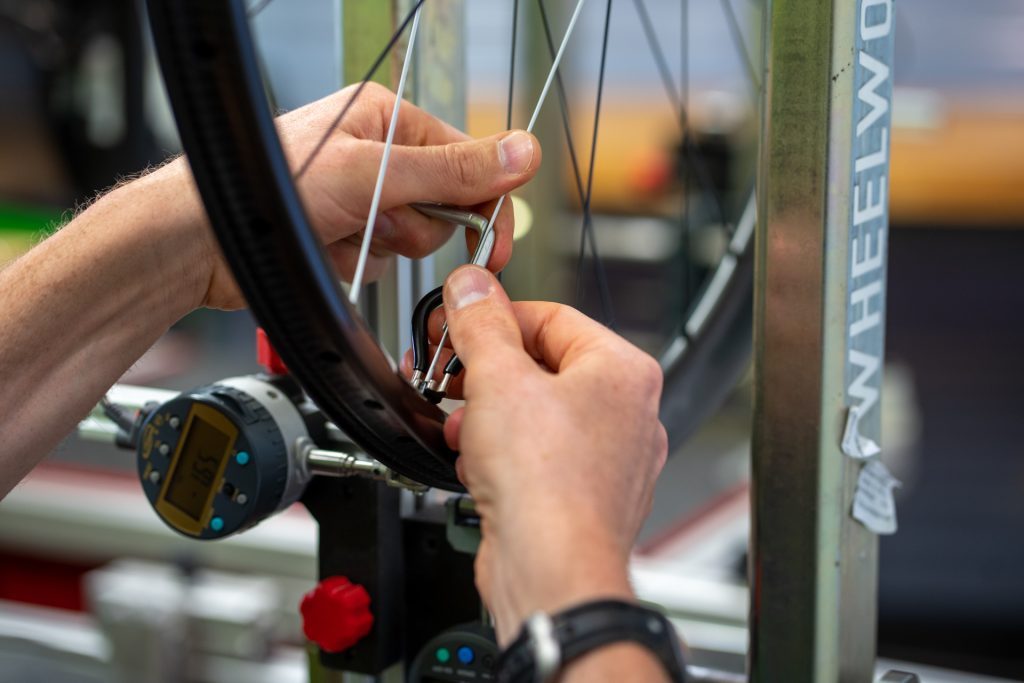
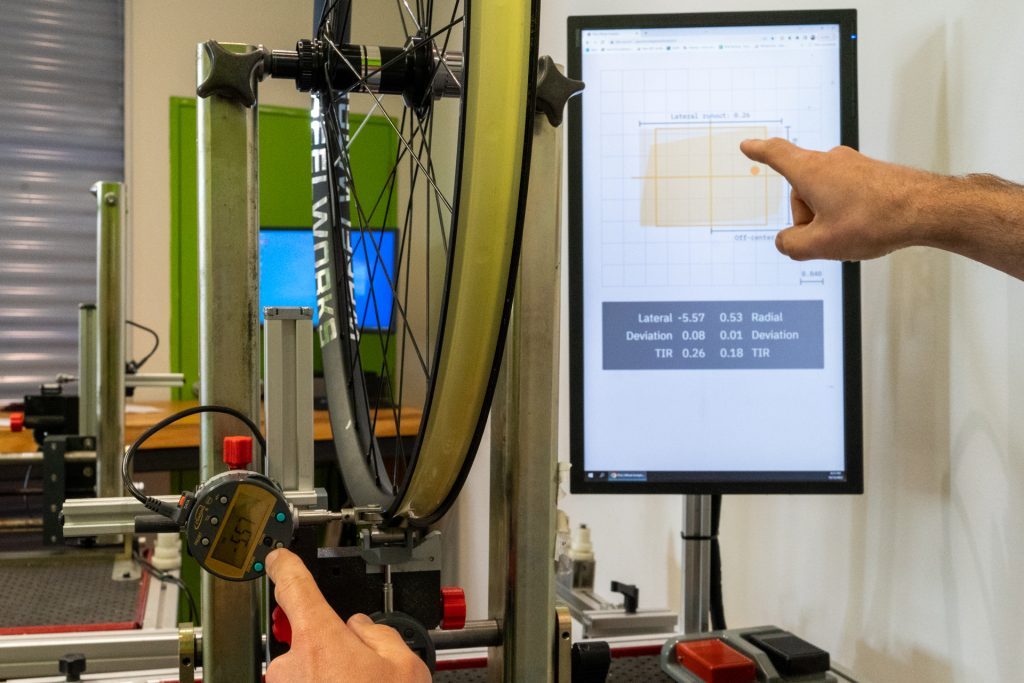
Stressed under pressure
Grimlock is a special tool we developed and built to pre-stress our wheels. If you’ve ever ridden a new bike or wheelset and heard pinging from the wheels, or if you’ve ever had a wheel go out of true or loose tension shortly after being built then you’ve seen inadequate pre-stressing.

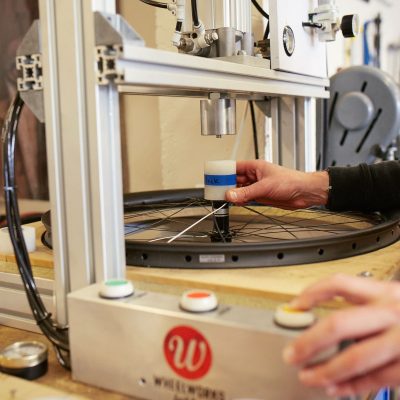
The most important detail that you can't see (but you will notice)
Accurate and exact spoke length reduces the likelihood of spoke breakage. This important detail is hidden but we still go to extraordinary lengths to ensure each and every spoke is the exact length needed, often using our Japanese made Morizumi machine to cut down to 0.1mm of accuracy and roll 10mm of beautiful new thread.
For more on what we do to avoid spoke breaking, check out our video Why Spokes Break.
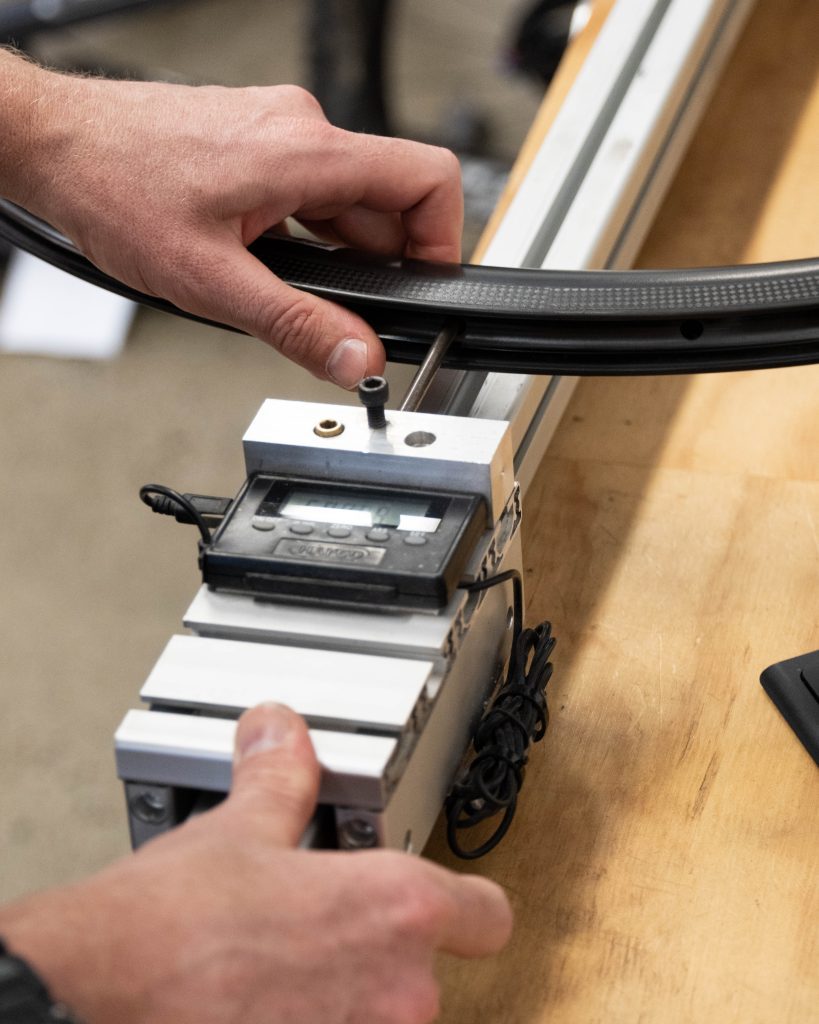
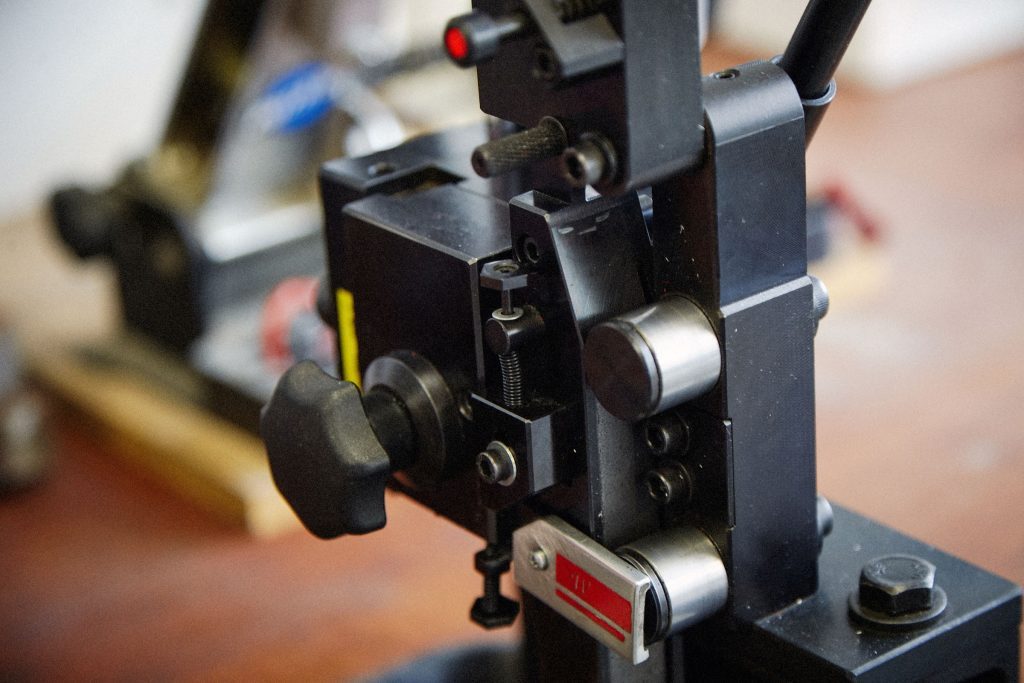
Wheels for life
We don't just build wheels that perform well - we build wheels for life. We worry about the thousands of details in each wheel, so you don't have to worry about anything while riding them.
While it's tricky to define the lifespan of each wheel, our goal is to maximise what's possible.
Using quality components, carefully designing and building a wheel that holistically performs to each customer's needs, a well looked after Wheelworks wheel will perform for thousands of kms.
Back in 2017 you guys built me a new set of FLITE wheels with a Son28 hub on the front and a Rohloff hub on the rear. Just last month I was doing an oil change on the Rohloff and was reflecting on the journey’s that these wheels have taken me on. They had 60,000km on them which has included a TA, 5,000km in Asia, 25,000km in North and Central America, the TD, a couple of GSB’s, K500’s plus a whole lot of other adventures.
This service was in prep for the Race to the Rock, a 3800km pilgrimage from Brisbane to Uluṟu (Ayres Rock) via Rockhampton. RttR is now done and the wheels are still turning true, the hubs are still running free and the Rohloff is just a dream to have on the bike.
This event was brutal on bike and body with some on the worst roads I’ve had the pleasure to ride. Day one I only managed to cover 230km but climbed over 6200mt. Day two didn’t let up with over 4500mt of climbing. This theme continued for the 990km to Rockhampton. Once turning inland things flattened out but the roads got worse and saw us riding 200km sections of corrugated Sandy roads that you just couldn’t find a flow on. They were a full body spanking. The outback was some of the harshest conditions I’ve ever rides through, with unrelenting heat, water 250+ km apart and regularly over 400km between resupplies the bikes were heavy and took a pounding.
Despite this the race was over in 12 days, 15 hrs, 35mins for 2nd equal and only 4hrs behind the winner.
Anyway a long winded way to say I’m still bloody happy with my FLITE wheels, Son Hubs and especially my Rohloff, which have now clocked up 64000km.
Because we know your Wheelworks will be rolling for years to come we commit to ensuring service parts are available and we even provide free brake pads for all Maker carbon rim-brake wheelsets, for life.
We provide tips and tricks on how to get the most out of your wheels, 'How To' videos and articles to look after and service your wheels, and if in doubt, we're here to help with any issues or questions.
With your unique wheel details easily to hand we are here to help should you need to service, re-decal, or upgrade/modify your wheels to fit for a new drivetrain or bike. It’s common for us to be having conversations and supplying parts for wheels built 5 or even 10 years ago.
We will check your wheels for trueness and tension at any time, at no charge. Our wheels are backed by our industry-first and industry-leading Lifetime Guarantee.
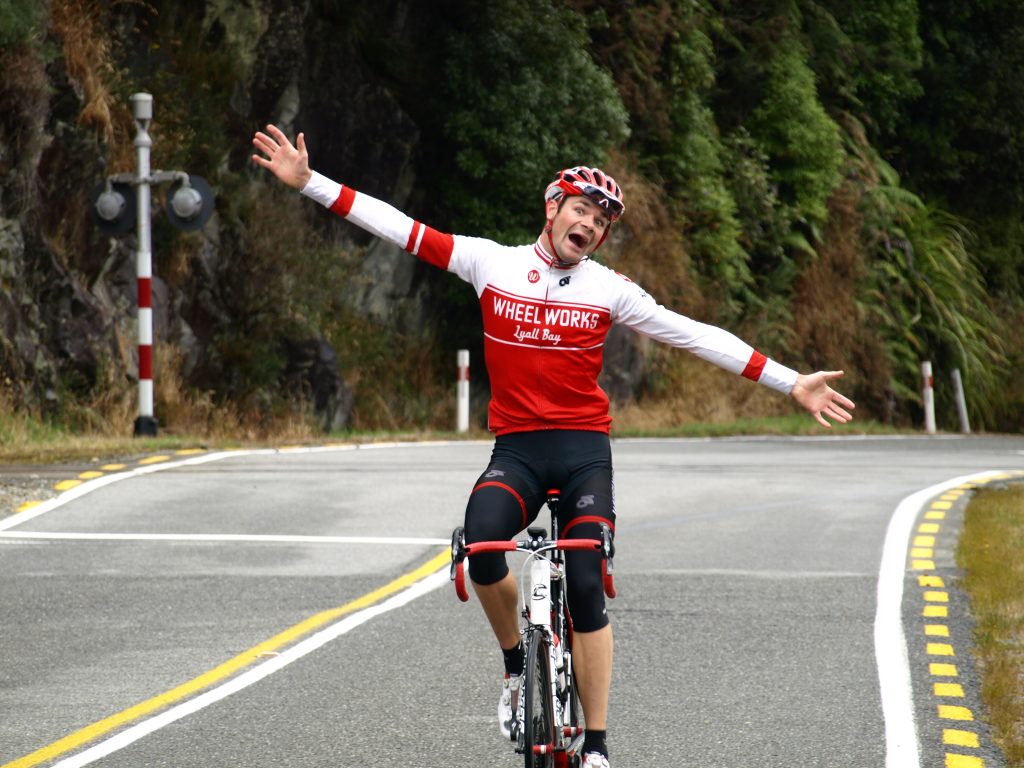
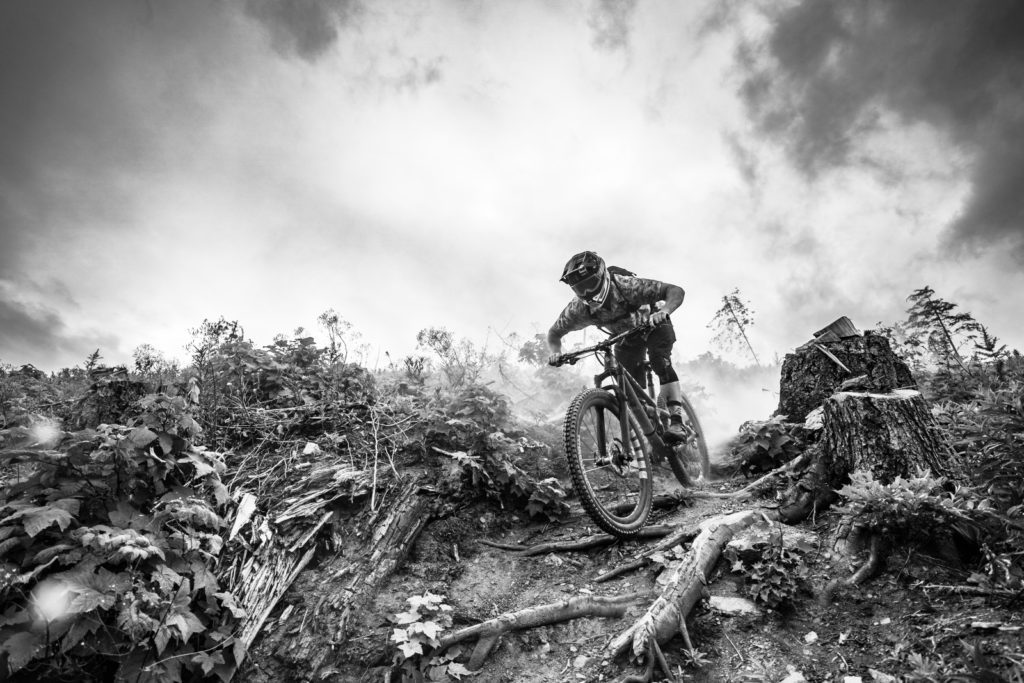
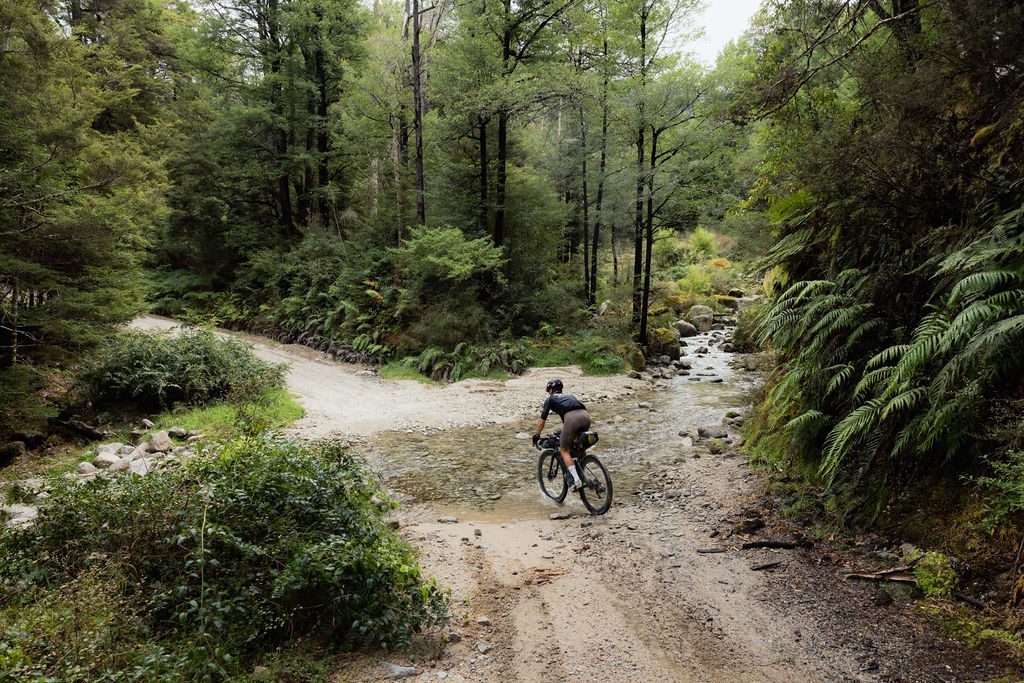
Have More Questions?
Chat with a friendly sales rep about the wheels we love!